熱處理托盤的生產周期縮短是可行的,需通過技術升級、流程優(yōu)化與管理改進相結合,在保證質量的前提下實現(xiàn)效率提升。以下是具體策略:
**1. 技術升級優(yōu)化工藝**
熱處理工藝是瓶頸。采用真空熱處理、感應加熱等技術可縮短加熱/冷卻時間。例如,高頻感應加熱可將升溫速率提升30%-50%,配合梯度控溫技術可減少保溫時長。同時引入自動化裝卸料系統(tǒng),將傳統(tǒng)批次處理改為連續(xù)式生產,設備利用率可提高40%以上。
**2. 數字化驅動的協(xié)同制造**
構建數字化生產線:使用CAD/CAE完成托盤結構輕量化設計,通過熱力學預判變形量,減少試制次數。部署MES系統(tǒng)實現(xiàn)物料與工序銜接,數控加工中心與熱處理設備數據互通,使機加工與熱處理準備期重疊,縮短等待時間20%-30%。3D打印技術可用于復雜結構托盤的一體成型,減少傳統(tǒng)焊接/組裝環(huán)節(jié)。
**3. 供應鏈與生產流程再造**
實施JIT模式,與特鋼供應商建立VMI庫存共享,將原料采購周期壓縮至72小時內。采用模塊化生產,將托盤分解為標準化部件并行加工,關鍵承重部位采用預制件,總裝時間減少50%。建立快速檢測通道,用激光三維掃描替代人工檢測,質檢效率提升60%且數據可追溯。
**4. 精益管理消除隱性浪費**
運用價值流圖分析識別非增值環(huán)節(jié),如傳統(tǒng)工藝中自然冷卻耗時長達8-12小時,改用水霧冷卻系統(tǒng)可將時間壓縮至2小時。推行SMED快速換模,模具更換時間從4小時降至45分鐘。通過TQM提前預防質量缺陷,返工率降低至2%以下。
**實施效果與風險控制**
企業(yè)案例顯示,綜合應用上述措施可使生產周期從28天縮短至12天,產能提升130%。需注意工藝變更需通過金相組織分析和疲勞測試驗證,初期投入成本約增加15%-20%,但6-8個月即可通過交付效率提升收回投資。建議分階段實施,優(yōu)先改造熱處理和檢測環(huán)節(jié),逐步向全流程延伸。
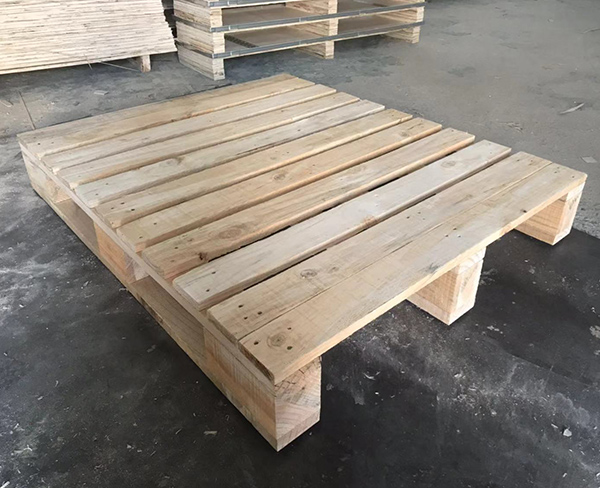
上一條:熱處理托盤如何應對振動沖擊?
下一條:沒有了